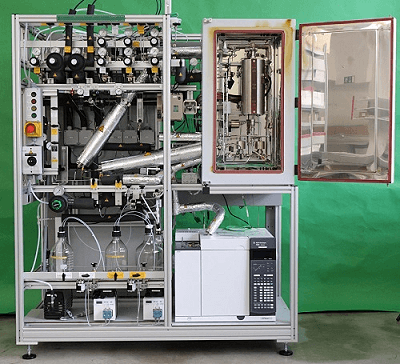
This micro reactor system offers an impressive range of functions for research and process development in the chemical industry as well as catalyst testing. With a tubular reactor that can withstand pressures of up to 100 bar at temperatures of 650 °C and 10 bar at 850 °C, it opens up a wide range of applications. The use of materials such as 1.4841 and quartz allows temperatures of up to 1000 °C. The system is equipped with an isothermal catalyst bed, 9 gas dosing units, 2 liquid dosing units with vaporiser, a hot air oven up to 190 °C to avoid condensation, a 3-zone reactor oven up to 950 °C, a vacuum pump, a condenser, a gas-liquid separator and a gas chromatograph. Automation is provided by a Simatic S7 controller and an operator PC with Simatic WinCC and a recipe control system.
Features:
- Pressure and temperature tolerance: up to 100 bar at 650 °C and 10 bar at 850 °C.
- Precise dosing: 9 gas dosing units and 2 liquid dosing units with vaporiser.
- Temperature control: Hot-air oven up to 190 °C to prevent condensation and 3-zone reactor oven up to 950 °C.
- All necessary accessories included: vacuum pump, condenser, gas-liquid separator and trace heatings.
- Endurance tests over several months with a pre-programmed sequence can be realized thanks to robust industrial automation.
- Highly automated: Simatic S7 control and operating PC with Simatic WinCC and recipe control system.
- A gas chromatograph with programmable measuring times and several measuring locations can be integrated.